Gigafactory opens: what Tesla can teach us about digitalization
In March 2022, the Gigafactory started operating. The high-tech factory is trailblazing in many respects. So, we explored what Germany can learn from the Gigafactory when it comes to digitalization.
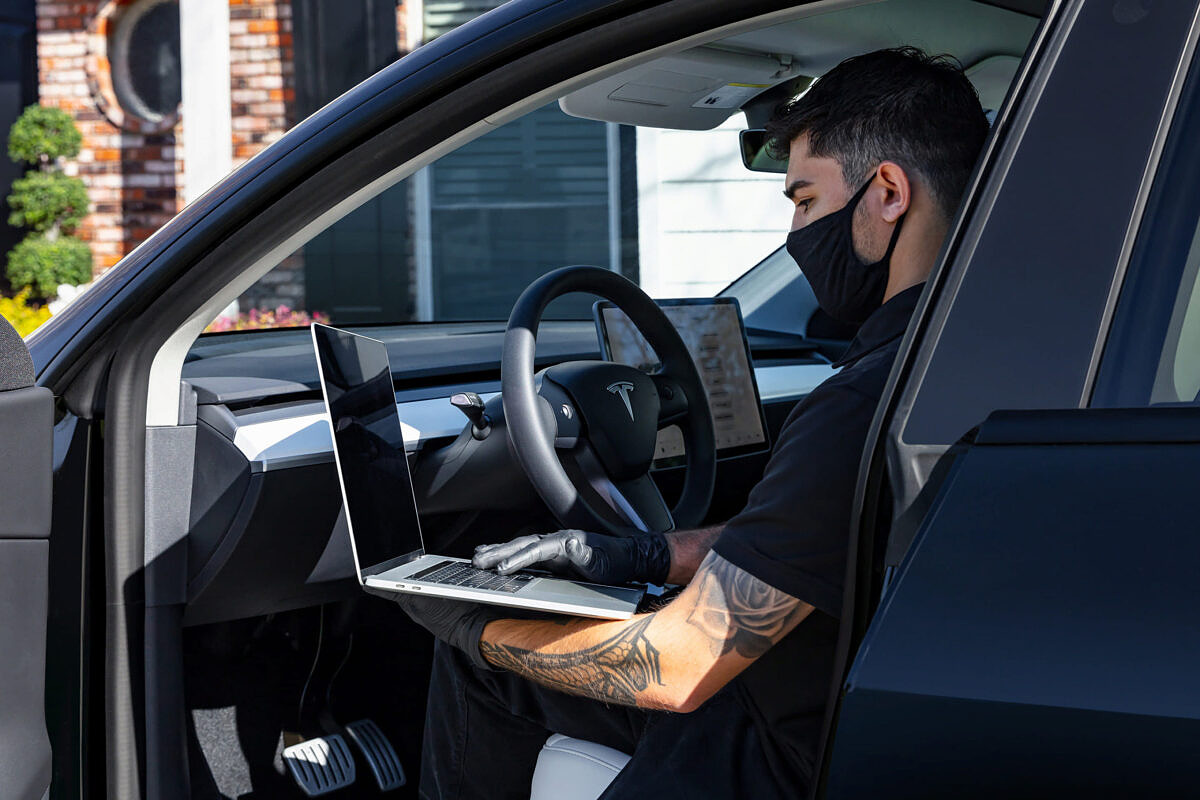
The Gigafactory is the most cutting-edge factory in Europe
It took just two years from the groundbreaking for the electric car factory in Grünheide (Brandenburg) for the first Tesla “Y Performance” vehicles to roll off the assembly line. The Gigafactory would have been neither conceived nor implemented without the visionary Elon Musk. The result is impressive: Tesla wanted to set new standards with the Gigafactory. In Germany, the country of carmakers of all places, a completely innovative showcase project materialized, leaving the industry giants in the dust. It’s not without reason that analysts estimate Tesla’s market value at around one billion U.S. dollars. That’s the value of the ten trailing automakers put together.
Tesla’s plans were even mocked by some. After all, Musk was wanting to redefine mechanical engineering in Germany of all places. Since March 2022, we now know what the future looks like. The future is digital, data-driven, intelligent, efficient, local, and incredibly fast.
AI-powered manufacturing efficiency – artificial intelligence and automation
Efficiency takes center stage at the Gigafactory. In that respect, it doesn’t stand out from other big automotive plants. However, it certainly stands out in terms of how it achieves this efficiency. Elon Musk leverages artificial intelligence. The principle is called “automating intelligently” and is a fusion of automation processes and AI technologies. The Gigafactory is thus a showcase project for Industry 4.0.
The role of the Tesla Cloud in practice
The concept is not yet fully developed, but the past few years have shown that Elon Musk is true to his word. For his electric fleet, he is planning to store driver profiles in the Tesla Cloud, among other features. These profiles are of great interest, especially for car sharing, because they would allow the seat and mirrors to be automatically adjusted to the user. Not only that, but software updates could also be easily carried out via the Cloud.
Vertical integration or in simple terms: do it yourself
Tesla uses its own parts. In this day and age, that’s unusual, yet at the same time harks back to the good old times. Tesla owns most of its supply chain. From the production of its batteries, photovoltaic systems, and car bodies right through to programming, everything is taken care of in-house. When you consider that nearly all its competitors have experienced difficulties with their supply chains recently, Tesla’s vertical integration approach could be a guarantee for success in uncertain times.
Speed at any price
Just a few kilometers from the Gigafactory stands Berlin’s BER airport, which took 14 years to complete. In contrast, the Tesla factory is a prime example of how quickly something can be built when a vision is realized without compromise. Germany’s digital transformation has been stalling for years and is constantly being pushed further and further back into the future – similarly to the BER airport.
It’s time to speed up the red tape, streamline processes, and roll up one’s sleeves instead of endlessly discussing digitalization without tangible results.
Glocal – global but local
Globalization is unstoppable and irreversible. And yet, events in recent years have shown just how vulnerable supply chains are. The fact that Tesla built its factory near Berlin, in the heart of Europe, is an important sign that low wages and production costs aren’t the be-all and end-all. This return to the roots is not just being observed in the tech industry – it’s a general trend. With a well-developed infrastructure, Germany will be able to keep up with any competition hands down; it simply needs to be much, much quicker in this endeavor.
If you don’t want to miss any other exciting topics, then subscribe to our content newsletter now and stay up to date.